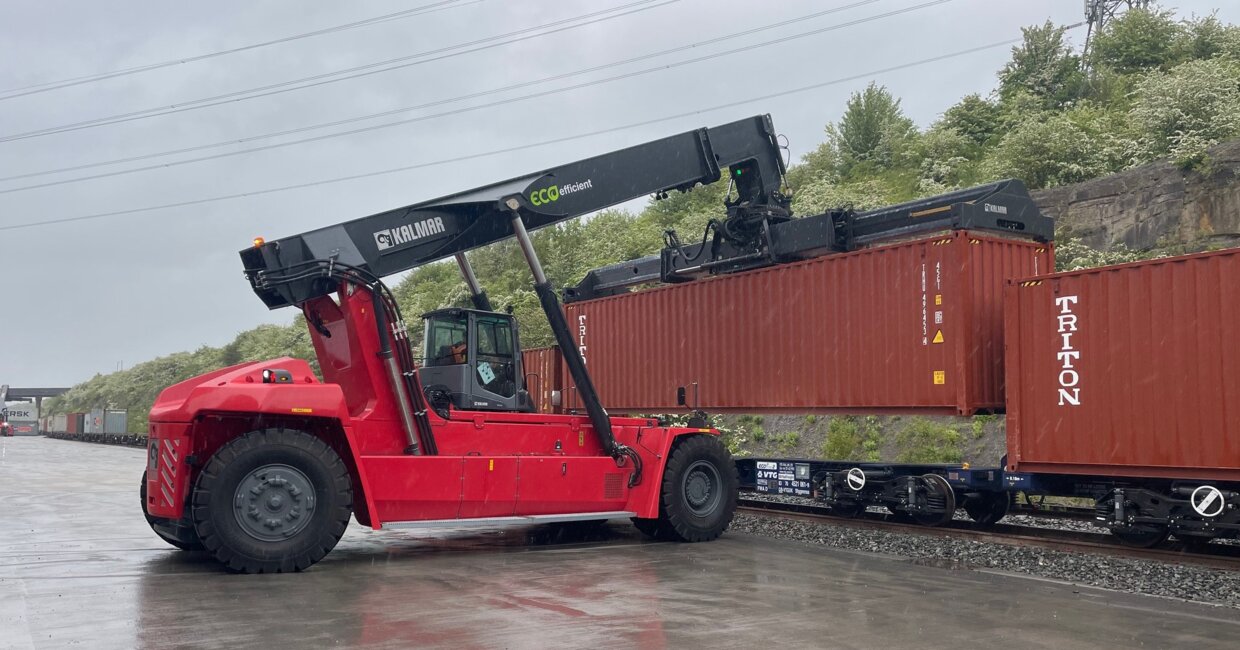
Newell & Wright embrace sustainability with innovative technologies
Newell & Wright use the Kalmar Eco Reachstacker and HVO100 to save fuel costs and help protect the environment.
Newell & Wright was one of the first cargo handling specialists in the UK to begin using HVO100 in their regular operations. They chose the Kalmar Eco Reachstacker which can use 100% Hydrogenated Vegetable Oil (HVO100) as fuel.
“We take sustainability very seriously,” says Stephen Newell, Operations Director for Newell & Wright Group. “We try to be at the forefront of new technologies and alternative fuels which increase efficiency and are better for the environment.”
New tech and fuels
Founded in 1974, Newell & Wright is based in Sheffield and has about 300 employees. They received their first reachstacker from Kalmar in 2008 and since then have been regular customers. Newell & Wright have a history of adopting technological improvements as they become available.
“In 2016 we bought a smaller machine from Kalmar with the HVT drive train. That was one of the early examples of next generation machines,” Newell continues. “Lowering carbon emissions and improving fuel efficiency were the big reasons why we bought the Eco Reachstacker four years later. Red diesel is disappearing in the UK so we need new solutions.”
The Kalmar Eco Reachstacker is an ultra-efficient container-handling machine.
The Kalmar Eco Reachstacker is an ultra-efficient container-handling machine. It can cut fuel consumption by up to 40% compared to 5-10 year old equipment and 25% compared to more recent models.
Yet the Volvo engine in the Eco Reachstacker can also use HVO as fuel. By combining HVO with improved fuel efficiency it is possible to lower CO2 emissions by about 90% compared to old machines.
HVO100 fuel is made from 100% renewable raw materials such as vegetable oils. It can be used as a replacement for diesel in some engines, such as on the Eco Reachstacker. One of the big benefits of using HVO100 as fuel is that it does not release any new CO2 into the atmosphere. The fuel is still not readily available everywhere, but it is becoming more popular. Newell & Wright have sourced HVO from a local fuel distributor in England.
Saving costs and the environment
Newell & Wright ordered their first Eco Reachstacker at the end of 2020 and started using it in May 2021. They have been so pleased with it they have ordered two more to be delivered in February and October 2022.
“Each machine has fuel savings of about 5-6 litres per hour. Each machine runs about 18 hours a day so you can see how big these savings are,” says Newell.
"That’s my favourite part of the Kalmar Eco Reachstacker: it has brought us fuel saving costs as well as being better for the environment.”
One of the keys to improved fuel efficiency is how the drive train and transmission operates with the help of smart software. At first, the drivers thought the new machines were slower, but Newell & Wright were able to take a look at the real-time data to see that they weren’t slower at all. The drivers just needed to get used to the way the drive train operates.
“We have Kalmar Insight so we can see live data on the machines” Newell explains. “Now the drivers love the driveability and the quietness of the Eco Reachstacker.”
Machines which use renewable HVO100 are a major improvement, but this is only one step towards full electrification.
“We are definitely waiting for reachstackers powered by electric motors or even hydrogen cells,” says Newell. “Of course, we look for technology which benefits the business. That’s my favourite part of the Kalmar Eco Reachstacker: it has brought us fuel saving costs as well as being better for the environment.”
Watch our Green Chair video, where our expert Niclas Samuelsson, sales & Product Strategy Engineer, Terminal Tractors at Kalmar, explains what HVO100 fuel is, why it is important, and what benefits it brings.
Related articles
Further reading
Customer case
Subscribe and receive updates in your email
Assine nossas publicações